
Oil & Gas
At Visser Precision, we recognize that the oil and gas industry operates in an environment unlike any other. The challenges of extracting, refining, and distributing energy resources demand a level of precision, reliability, and innovation that few manufacturing solutions can match.
Additive Manufacturing
Additive Manufacturing (AM), also known as 3D printing, has emerged as a transformative technology in the Oil & Gas industry, offering numerous benefits across various segments of the sector. Traditionally, the industry has been characterized by large-scale manufacturing processes and complex supply chains. However, AM introduces a shift for oil and gas companies by enabling the rapid production of customized components, reducing lead times, and enhancing operational efficiency.
How Does Additive Manufacturing Support the Oil and Gas Sector?
Additive Manufacturing (AM) plays a key role in supporting the diverse needs of the Oil and Gas sector by providing precision fabrication solutions tailored to withstand the rigors of harsh environments.
Precision Fabrication for Tough Environments
Metal additive manufacturing offers a versatile approach to fabricating components that excel in the demanding conditions encountered in oil and gas operations. With our skilled machinists and cutting-edge equipment, we ensure that every component we produce meets the highest standards of quality and performance.
From components for exploration rigs and downhole tools subjected to extreme high temperatures and pressures to spare parts required for the maintenance of refining facilities, our products are engineered to endure the challenges posed by the industry's toughest environments.
By leveraging additive manufacturing technologies, we can manufacture parts with intricate geometries and complex designs that are precisely tailored to meet the specific requirements of each application, ensuring optimal functionality and reliability.
Tailored Solutions for Every Need
Whether you need highly complex 5-axis spindles or essential yet intricate parts, our metal AM capabilities enable us to provide customized solutions that precisely match your specifications.
We understand that the Oil and Gas sector encompasses a diverse range of applications, each with its unique challenges and requirements. Our ability to deliver tailored solutions ensures that you receive components optimized for efficiency and performance, regardless of complexity.
Compliance and Quality Assurance
Compliance with regulatory standards is paramount in the Oil and Gas industry, where safety and reliability are non-negotiable. Our additive manufacturing processes adhere to the strictest legal standards and industry regulations, ensuring full compliance and adherence to quality assurance protocols.
By maintaining stringent quality control measures throughout the metal 3d printing process, we guarantee the reliability and integrity of our components. Our commitment to quality assurance gives you peace of mind, knowing that even the most complex parts meet or exceed the highest industry standards.
Applications of Additive Manufacturing
Prototyping and Design Validation
AM enables rapid prototyping of components and equipment, allowing engineers to iterate designs quickly and cost-effectively. By producing functional prototypes directly from digital models, metal AM accelerates the product development cycle and facilitates early-stage design validation.
Spare Parts Manufacturing
One of the significant advantages of AM in the Oil & Gas industry is its capability to produce spare and replacement parts on demand. Instead of maintaining costly inventories of spare components, companies can leverage 3D printing technologies to manufacture parts as needed, reducing lead times and inventory costs. This approach ensures equipment uptime and minimizes disruptions to operations.
Equipment Customization
AM enables the customization of equipment and components to meet specific project requirements or operational challenges. From custom fittings and connectors to complex manifold systems or housings systems, AM allows for the creation of tailored solutions that optimize performance and reliability in diverse applications.
Reducing Weight and Material Usage
AM facilitates the production of lightweight components without compromising strength or structural integrity. Oil and gas partners can choose from a variety of metals and alloys when designing their components, which can also contribute to overall component weight. By optimizing designs and reducing material usage, AM contributes to weight and operational cost savings in equipment and structures, which is particularly advantageous in offshore and remote operations where transportation costs are a concern.
Our equipment is capable of complying with the most stringent legal standards in a variety of sectors. Whether you need extensive machine work such as 5-axis spindles or just a simple part machined, we can help.
Advantages & Limitations
Advantages
Additive Manufacturing (AM) offers several significant advantages for the Oil & Gas industry:
On-Demand Production
AM enables on-demand production of spare parts, reducing the need for large inventories and minimizing downtime. This capability is particularly beneficial for remote or offshore operations where access to traditional manufacturing facilities may be limited.
Customization and Design Flexibility
AM allows for the production of highly customized components tailored to specific project requirements. Complex geometries and integrated designs can be realized with AM, optimizing performance and functionality without the need of excessive machining.
Supply Chain Optimization
By manufacturing components in the United States AM reduces reliance on external suppliers and streamlines the supply chain. This reduces lead times and transportation costs, particularly within the US, where our 3d printers reside.
Consolidation of Components
AM enables the consolidation of multiple parts into single, integrated designs. This reduces assembly time, minimizes points of failure, and simplifies maintenance and repair procedures.
Rapid Prototyping and Iterative Design
AM accelerates the product development cycle by enabling rapid prototyping and iterative design processes. Engineers can quickly test and refine designs, reducing time-to-market and improving product performance.
Limitations
However, the widespread adoption of AM in the Oil & Gas industry faces several challenges:
Material Qualification
Ensuring the reliability and performance of AM-produced parts requires rigorous material qualification processes. This involves testing materials for mechanical properties, chemical resistance, and environmental durability to meet industry standards.
Regulatory Compliance
Compliance with regulatory requirements and industry standards poses challenges for AM adoption. Certifying AM-produced components for use in critical applications requires alignment with stringent safety and quality assurance protocols.
Scalability
Scaling up AM production to meet the demands of large-scale industrial operations remains a challenge. Production rates, build volume limitations, and equipment capacity need to be addressed to fully realize the potential of AM in high-volume manufacturing.
Cost Considerations
Despite advancements in AM technology, the cost of AM-produced components may still be higher than traditional manufacturing methods for certain applications. Cost-benefit analyses are required to justify the investment in AM technology and ensure economic viability.
Request a Quote
Ready to elevate your oil & gas endeavors with Visser Precision? Contact us today to request a quote and discover how our expertise can propel you toward victory.
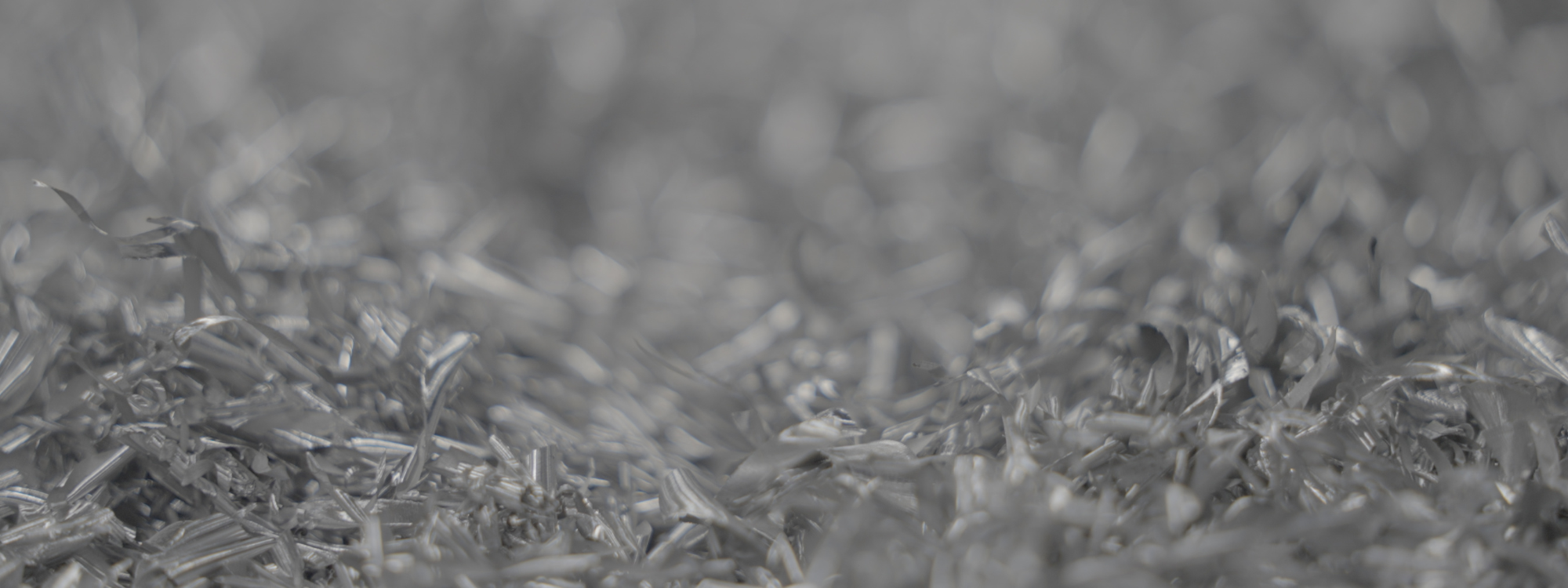
let’s get social
Join us on social media to stay updated on the latest developments in how additive manufacturing can transform the oil and gas industries. Connect with our community, access exclusive content, and discover how Visser Precision can enhance your operations.